
Electrolysis is a proven technology for permanent hair removal allowing people to live a life free of unwanted hair, which can arise from a variety of factors including hormonal imbalances, medications, gender dysphoria and hereditary factors. When each individual hair is treated with an electrical current it creates a chemical reaction that removes the follicle’s ability to grow. Electrolysis is a superior method of hair removal compared to laser, flashlamp or IPL as it is suitable to all skin types, safe for treating moles and tattooed skin and is the only permanent method approved by the FDA.

The Permanence electrolysis system works by applying a negative current to the hair follicle. Any moisture present in the follicle is converted into sodium hydroxide over a few minutes, killing the follicle. The electrical circuit is created via a conductive pad applied to the arm or leg and the application of a hair-thin metal probe into the follicle. The probe and pad are connected to the Permanence machine that can run up to 16 probes simultaneously, allowing treatment of up to 200 hairs per hours.
​

The key challenge for this project was a strategic requirement to build the product using electronics only, with no embedded software. Genesys developed the electronics for this device including an analogue electronics interface to the probes, which are connected via a port at the back of the device and the pad connected at the front. Key functions included dials for setting the current level and duration for each probe, and a variety of indicators for the status of each channel, including LEDs and buzzers.
​
As a medical device, the system had to be safe to use. In particular the system needed to ensure that the total current output of the probes is always at a safe level, disabling the output to the patient if any fault is detected. The system needed to be easily calibrated, requiring a test interface to support manufacturing and testing at the manufacturing facility.
​
Permanence launched the product in the United States as the GEMM-16.
Skiant Holdings provided commercialisation strategy, project management, engineering, compliance and manufacturing for this product.
​
Contact us to find out more about this project
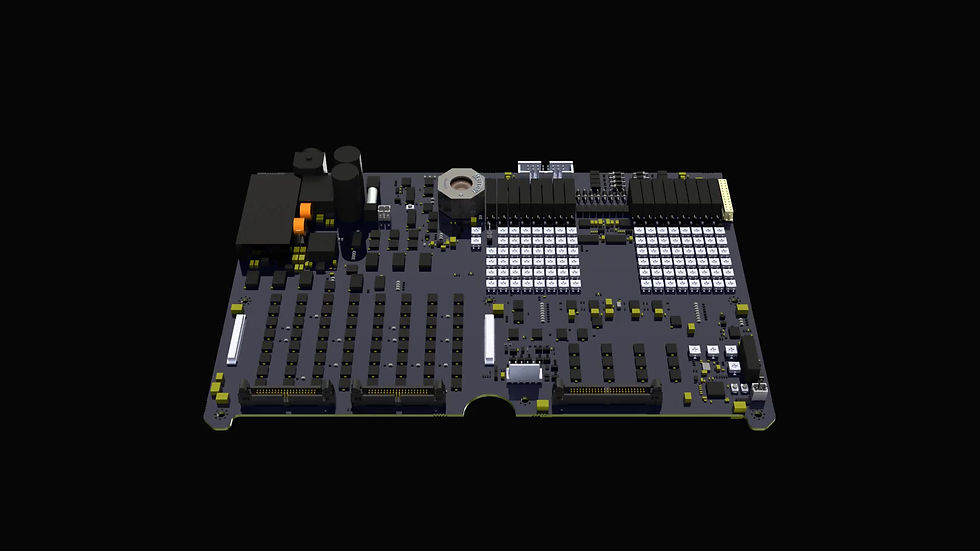